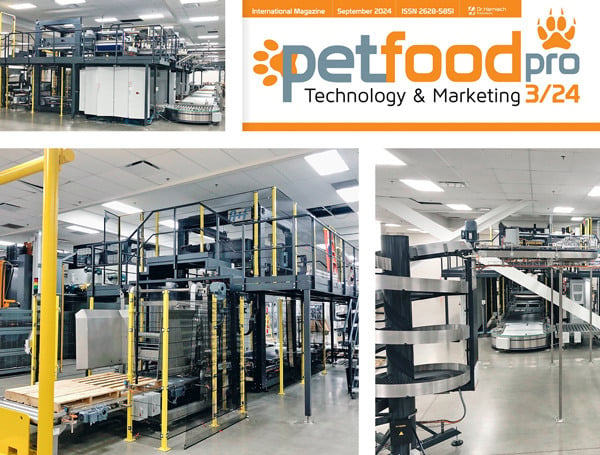
From two to four lines
Bremen-based saturn petcare GmbH expands in the USA - with palletizers from Germany
The market for pet food is attractive, especially for wet food for dogs and cats. A visible sign: Bremen-based saturn petcare GmbH has simply doubled its production lines in America from two to four. The palletizing system was brought over from Germany. Performance, flexibility and excellent practical experience played decisive roles in this decision.
The global pet food segment has recorded significant growth in recent years. According to market researchers from statista, turnover is expected to reach around 140 billion euros in 2024. They even expect the market to grow by more than five percent annually until 2028.
The drivers of this trend include demographic change, the increase in the number of single-person households and the significant rise in disposable income. The "humanization of pets" is cited as another factor. High-quality raw materials, natural ingredients and "superfoods" are currently also in high demand in pet nutrition. Last but not least, the number of pets has simply increased during the COVID-19 pandemic.
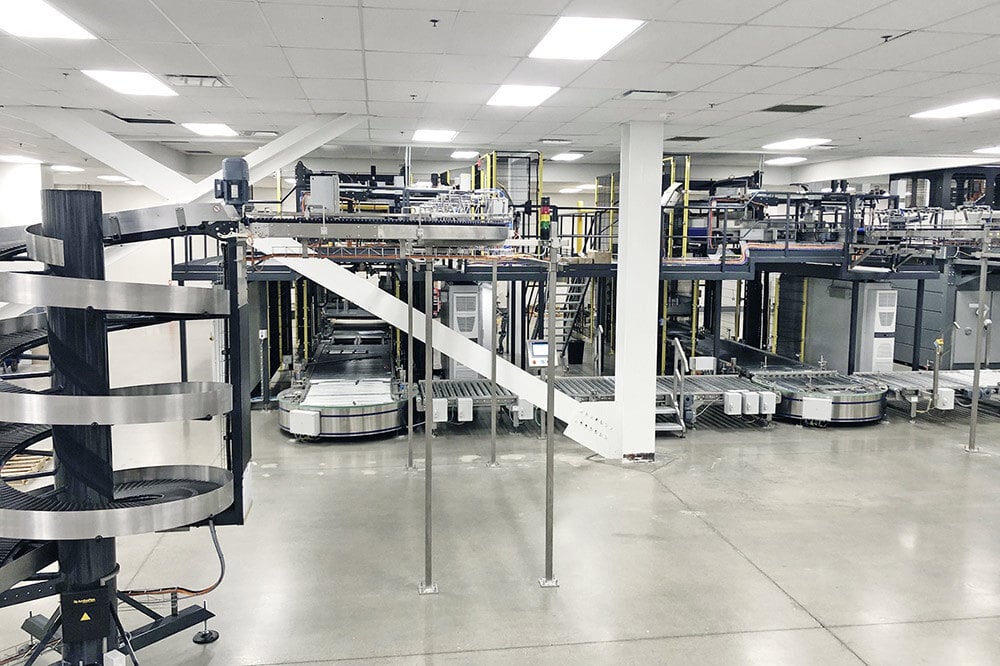
The order comprised the necessary conveyors including spiral conveyors, the integration of the two palletizers, the automation and clarification of the interfaces as well as the commissioning including operator training.
Almost identical system in use in Bremen since 2021
saturn petcare GmbH, which is part of the Heristo Group, is a company that is extremely successful internationally in this field. Its plant at its headquarters in Bremen was established in 1991. Since then, wet food for dogs and cats has been produced here for the retail trade on ultra-modern production lines. Customers are mainly food chains that sell saturn products as private labels. The production plant is IFS-certified and therefore meets the highest standards in terms of quality and product safety. With documented success: Stiftung Warentest took a close look at cat food in 2020, for example. The result: six of the eight best products came from saturn petcare, in 2024 even 4 out of 5.
In addition to Germany, saturn petcare has production sites in the Netherlands and, since 2021, also in the USA, which is currently probably the strongest global market in terms of sales. As part of this expansion, a state-of-the-art production facility for wet food was built at the Terre Haute site in the state of Indiana, which was expanded from two to four production lines in 2023. The plan was to mirror the facilities on a one-to-one basis. This was also implemented - except for the two palletizers. Harald Knaup, Project Manager at saturn petcare in Bremen, looks back: "The reason for this decision was the palletizing concept, the design, the additional add-ons such as condition monitoring, layer pattern generator or the maintenance manager, the attractive price-performance ratio and, last but not least, the good experience we have had with the almost identical system here in Bremen since 2021." According to Knaup, another plus was the layer pad inserter, which can be loaded with new material without the palletizer coming to a standstill.
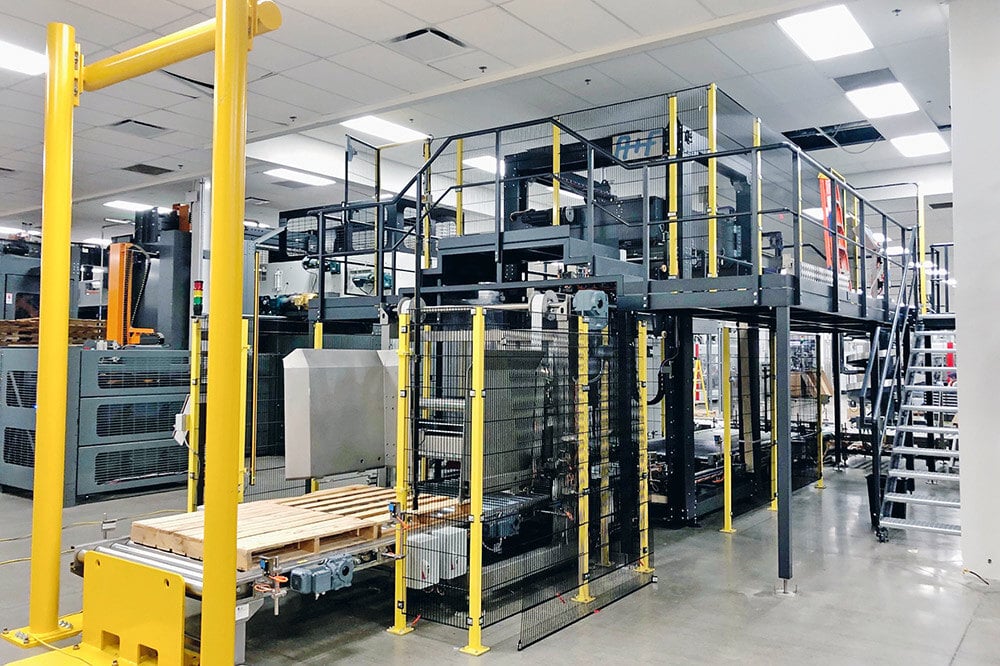
The palletizers work according to the "lifting pallet" principle. They are able to process very high loads and achieve an output of up to 280 layers per hour.
A "push of a button" is all it takes to change over
Both the palletizer in Bremen and the two in the USA work according to the "lifting pallet" principle. They are able to process very high loads and achieve an output of up to 280 layers per hour. Due to the extensive use of servomotors and thus the absence of pneumatics, the machines palletize very energy-efficiently. They are also highly variable thanks to the "layer pattern generator". The desired layer patterns are stored here. A "push of a button" is then all it takes to change over. The tool also supports the optimization or development of a layer pattern.
Understandably, there were some country-specific changes compared to Bremen and the USA. For example, the US standards had to be verified and the operating language and pallet format adapted. The power supply in the USA is also different at 120 volts. A corresponding transformer was installed in Germany in order to be able to test the electrics and controls in advance. Keyword control system: "What is unusual for America is that we used the Siemens S7 control system. This was initially discussed. But now they are extremely satisfied," summarizes Knaup.
A total of eight 40-foot containers shipped
Physical transportation was also a factor: the system was dismantled into the largest possible parts and stowed in eight 40-foot containers. The last of these began its journey by ship to New York on August 22, 2023. From there, it was transported on heavy-duty trucks over more than 1,000 km to Terre Haute, where assembly began on 16.09.2023. The construction site was managed by a mechanical supervisor, an electrical supervisor and a commissioning engineer. They were supported by five mechanics and three electricians from saturn petcare. In future, the system will be managed by the US company Standard-Knapp and via the Internet from Germany. "A clear signal of the international competence and expertise of the EOL Group," emphasizes Knaup.
Modern communication as an important tool
Specifically, the order included the necessary conveyors including spiral conveyors, the integration of the two palletizers, automation and clarification of the interfaces as well as commissioning including operator training. This complete package was handled on a turnkey basis. Important tools in this transatlantic collaboration were the modern communication options and construction site management with LOP 4.0.
LOP 4.0 is a cloud-based system that can be accessed by all project participants. This digital platform maps the project status during the construction site phase, from delivery to commissioning, with the greatest possible transparency. LOP 4.0 is also an open communication and documentation platform. Each project partner can, for example, upload photos or videos, post next steps for discussion or prioritize individual points. This ensures that the status of all project components is always up-to-date and clearly understandable. Interactions on the further course of the project are immediately visible. This reduces friction and coordination losses and leads to a high degree of predictability.
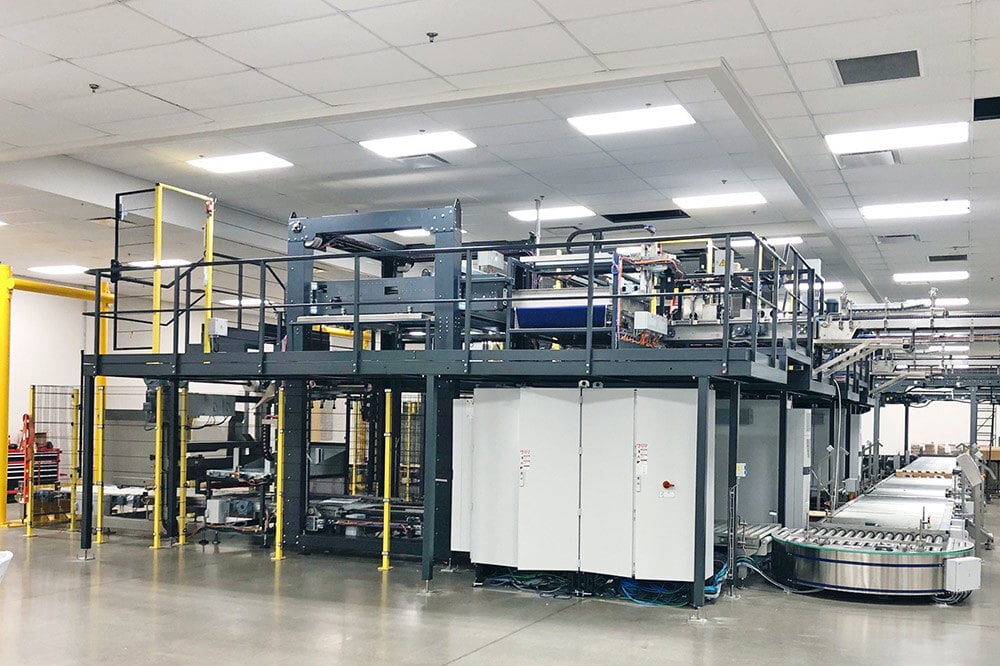
Maximum flexibility: The palletizers either run two products in parallel or each run the same product, or only one of the two is in operation.
"A thoroughly harmonious and focused collaboration"
The successful acceptance followed on 31.10.2023. "It was a thoroughly harmonious and goal-oriented collaboration," sums up saturn petcare. Since then, the two palletizers have each taken over two carton formats from upstream filling and packaging systems in which different types of pet food are packaged. In the infeed area of the palletizers, the incoming cartons are rotated and positioned according to the desired layer formation. This creates layer patterns that can be individually adapted by the customer. The pallets stacked in the palletizer are then transported to the delivery point via the pallet conveyor and conveyed from there to the warehouse. The pallets, in turn, are fed automatically via a magazine. The two palletizers transport both products in parallel or the same product, or only one of the two is in operation. They are therefore not only powerful and reliable, but also very flexible to use. And in view of the forecast growth scenarios, this is a really reassuring prospect.