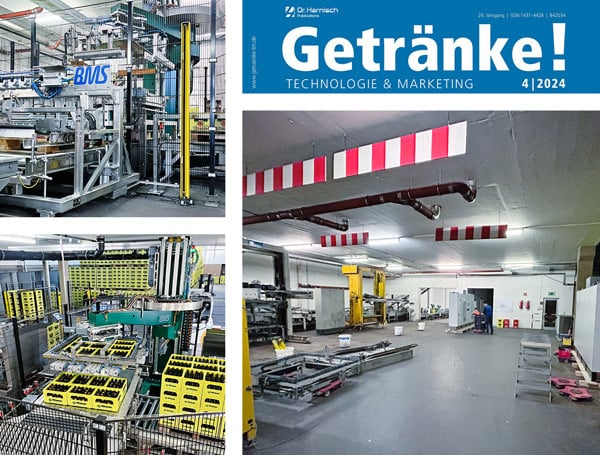
3-D puzzle
Demanding spatial conditions pose major challenges for the new palletizing facility at the Wittmann brewery - they are solved
Brauerei C. Wittmann OHG, Landshut, is a medium-sized private brewery that has been family-owned for five generations. It emerged from the breweries "Zum Heiß" and "Zum Dräxlmair". The history of the "Zum Dräxlmair" brewery can be traced back to 1616. In 1905/06, the brewery, which at that time was still located in the center of Landshut, was relocated to the outskirts of the city, where it is now located in the middle of the Achdorf district. However, the administration, which is now located in the historic Etzdorf-Palais in Ländgasse, had to be relocated.
As a specialty brewery, the Wittmann brewery supplies its customers within a radius of around 50 to 70 km around Landshut. It is a classic full-range supplier of top and bottom-fermented beers and non-alcoholic beverages. The Wittmann brewery has a tradition of very high standards for the quality of its raw materials and brewing technology. Many DLG awards such as the "Preis der Besten" and 70 other gold awards are the result of this philosophy.
"The next logical step we had to take"
Another important component of this success is the constant investment in environmentally friendly and quality-oriented machine technology. The Wittmann brewery is currently replacing its entire bottling process in a multi-phase project. The first step was the implementation of two state-of-the-art portal packers in the existing line. The complete rebuild of the palletizing system then began in 2023. Florian Drißl, 1st Brewmaster at Wittmann, looks back: "The existing palletizing system was from the end of the 1970s. The spare parts and maintenance situation was correspondingly difficult. It was simply the next logical step we had to take on our way to the new bottling line."
Only the premises of the old plant were available
The brewery had defined very clear specifications for the actual implementation: The palletizing system had to be able to effortlessly supply the future filler with 30,000 bottles per hour, offer maximum operational reliability overall, be automated according to the state of the art and include a crate turning station and a pallet check - all at the identical location of the old system. With regard to the pallet, there was also another task to solve. "As a medium-sized company with our own fleet of vehicles, we can still afford the brewery pallet, which is more attractive in many respects. However, we also have to deliver smaller batches on Euro pallets. These were loaded manually in the old system. The new system should be able to do this automatically," explains Drißl.
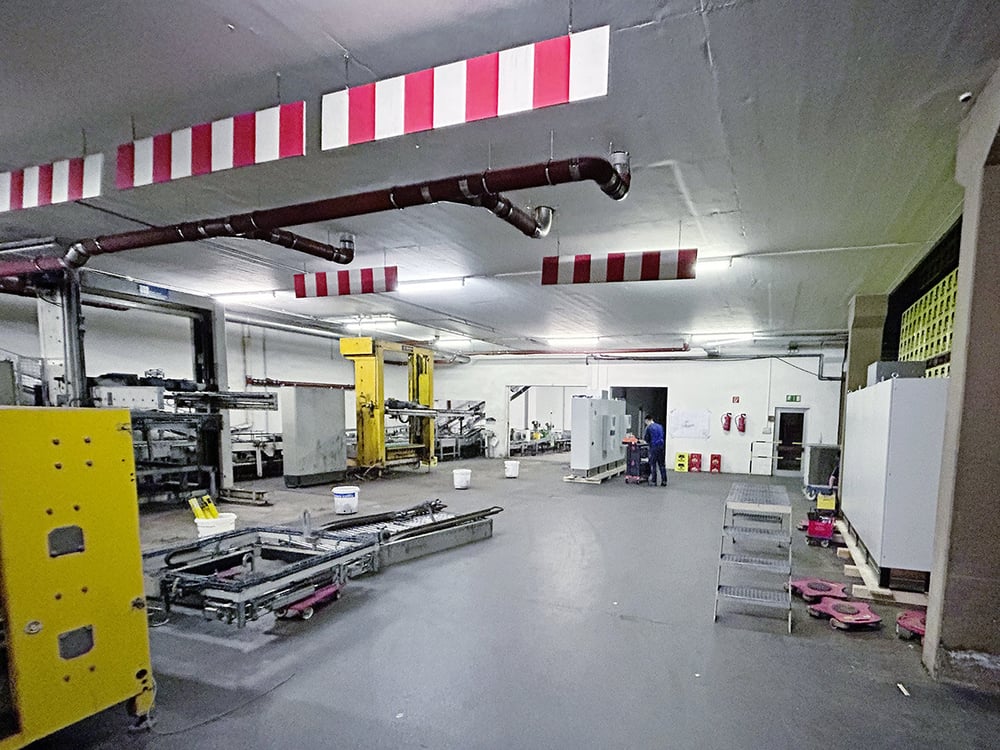
A ceiling height of 3.80 meters, limited space, more functionality - planning the new palletizing system at the Wittmann brewery proved to be extremely challenging.
A ceiling height of just 3.80 meters
A key challenge in the planning and implementation of the project was the spatial conditions. This primarily applied to the low ceiling height of just 3.80 meters. This meant that only column palletizers were possible. But even these were too high in their standard design. In addition, the required turning station and pallet control elements had to be placed in the specified area. Last but not least, the interfaces had to be prepared for the modified transport routes of the new filling plant. "With this wealth of restrictions and specifications, applicants dropped out of the tender directly. They didn't have the confidence to do this with their portfolio or didn't want to put in the extra effort required for customization," says Drißl.
Modified structure reduces column height
This 3D puzzle of room height and surface area was solved with a special version of the UNIPAL type 108 column palletizer. Components such as the drive technology, cable routes or valve terminals, which are normally positioned at the top of the column, were mounted to the side or underneath. In this way, the necessary height reduction was achieved in order to be able to install the two palletizers at Wittmann. The reduced height also offers another major advantage: the column palletizer can be transported upright on a truck. Brewmaster Drißl summarizes: "This is better in that I don't have to dismantle the column, I can leave the gripper head on, for example. I can also load and unload it more easily and bring it in - all in all, that means around two to three days less assembly time for us."
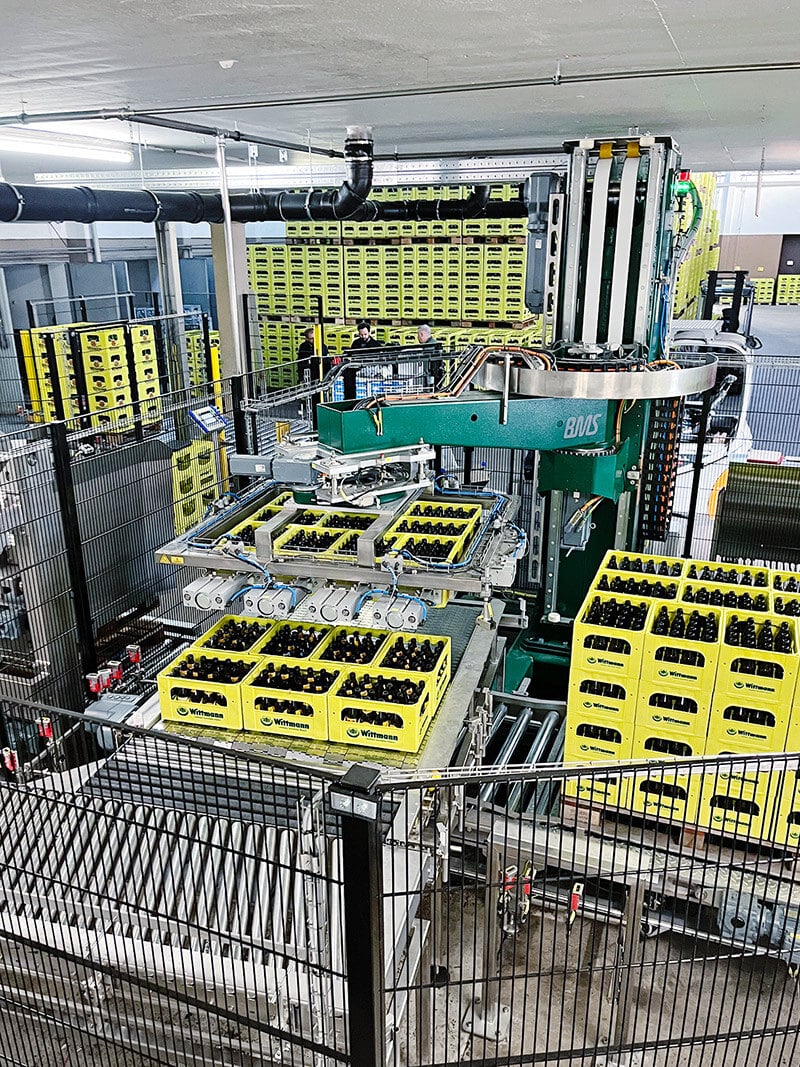
Thanks to a new construction, the height of the pillars could be lowered so that 3.80 meters was sufficient. But there is still not much space towards the ceiling.
The unloader is designed for an hourly output of 39,000 bottles and the loader for 36,000. The conveyors, the storage tables, the control system and the pallet control system were also supplied. The subsequent integration of a pallet binder and the interfaces to the future bottling line have already been prepared. The entire package, including dismantling, assembly, commissioning and training, was completed on a turnkey basis. The Wittmann brewery was responsible for the construction.
Virtual construction site management proves its worth once again
The contract was awarded in May 2023. Assembly in Landshut started on 23.01.2024 and the first bottles were filled on 12.02.2024. "We had scheduled three weeks for the entire project, including dismantling and on-site preparation. We absolutely stayed within this time frame," explains Drißl. The LOP 4.0 construction site management system made a significant contribution to this rapid implementation. LOP 4.0 is a cloud-based construction site management system that can be accessed by everyone involved in the project. This digital platform maps the project status during the construction site phase, from delivery to commissioning, with the greatest possible transparency. LOP 4.0 is also an open communication and documentation platform. Each project partner can, for example, upload photos or videos, post next steps for discussion or prioritize individual points. This ensures that the status of all project components is always up-to-date and clearly understandable. "We had already had positive experiences with LOP 4.0 with the packers. It simply has the advantage that nothing falls by the wayside thanks to the up-to-dateness and transparency," emphasizes Drißl. Speaking of packers: these had two further interactions with palletizing. Firstly, the palletizer can now also be accessed via remote maintenance. Drißl summarizes the second as follows: "This first collaboration was completely smooth and the machines are running excellently. We simply had the confidence that it would be the same with the palletizing. And that has been confirmed."
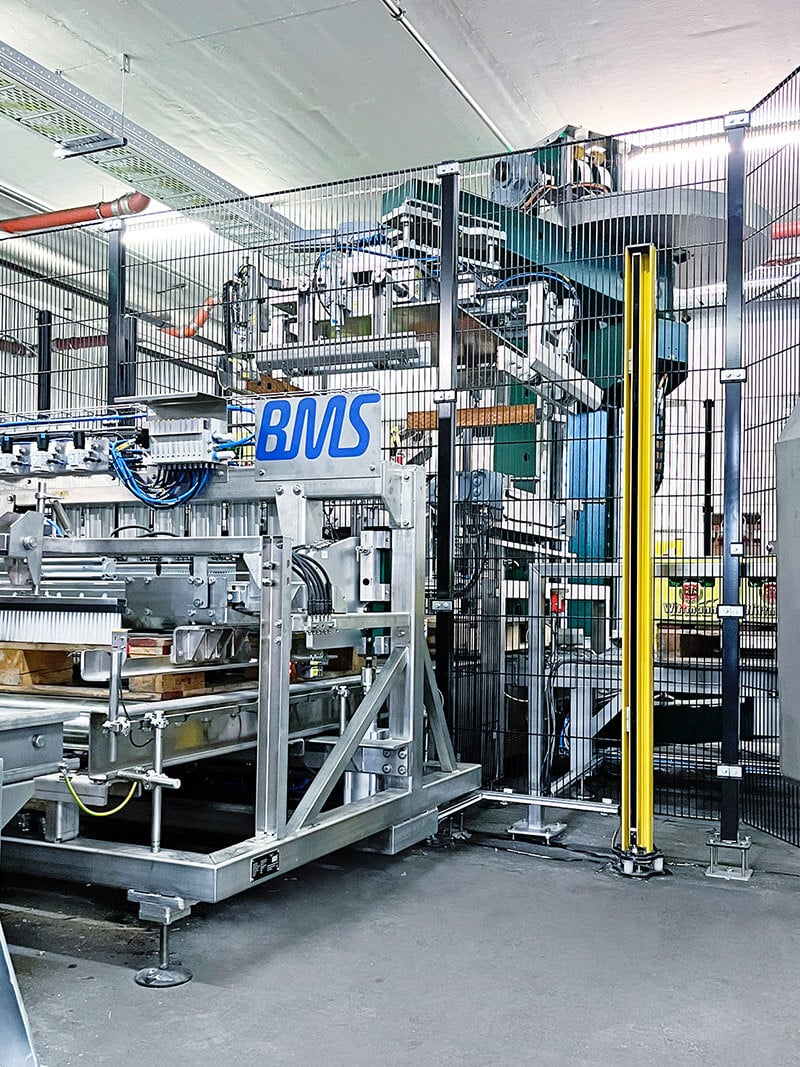
A pallet inspection system was also installed for the first time on the identical area of the old system.
Euro pallets are simply fed in during operation
The entire system has been proving itself in daily operation since the end of March 2024. A 20-module crate, two 24-module crates and an 11-module lemonade crate are processed. The latter has a special feature: It is only about half the size of the other crates and therefore has to be rotated for palletizing. "With the old system, we often had to use staff to help with this so that the crates didn't jam. This now works automatically and completely smoothly with the new system," says Drißl happily.
With regard to the pallets, both brewery pallets and Euro pallets can be loaded and unloaded as required. These can be fed into the new system at any time "at the touch of a button" via the reject pallet magazine and are then available for palletizing. Drißl explains the advantage: "We don't have to change pallets in the palletizing system to be able to process a small batch of around 30 Euro pallets. This not only saves us from having to place the full load by hand, but also a changeover time of 45 minutes." However, the system is also already designed to process mainly Euro pallets if the market demands this. In this case, the brewery pallets are fed in via the pallet magazine.
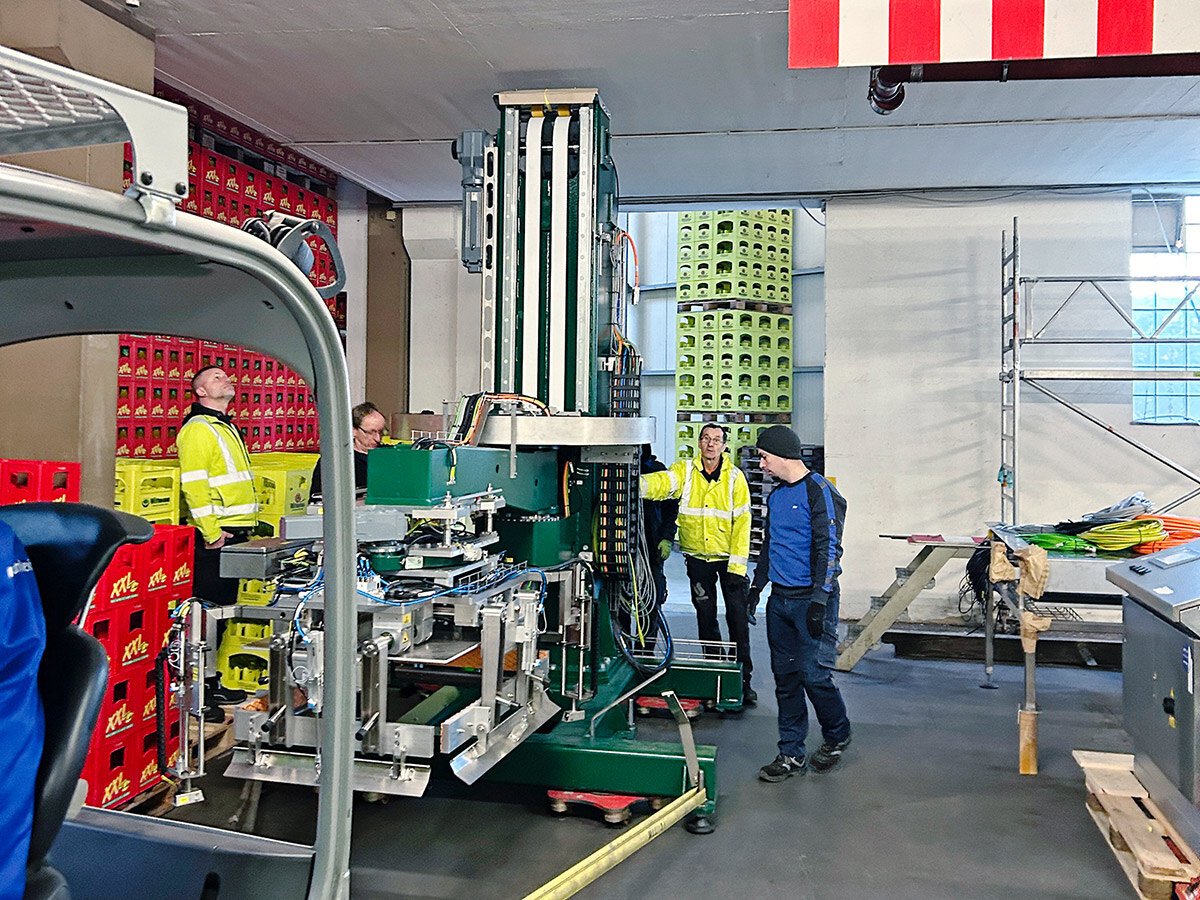
A lower column height also means that the palletizer can be transported upright. This significantly reduces transportation, insertion and assembly work.
"What was agreed was fulfilled in full"
In a nutshell: The new palletizing system at the Wittmann brewery reliably delivers the required performance despite the challenging spatial conditions, the problems with the turning station no longer exist, the pallet control offers more safety and the Euro pallets can now be fed in fully automatically during operation. An assessment that master brewer Drißl is happy to confirm after the practical experience gained with the system: "What was agreed was fulfilled in full. We are absolutely satisfied. The palletizing system will certainly not stand in the way of possible follow-up projects."